ヨコハマタイヤ
マニュファクチャリング
(タイランド)
PC・LT工場第3期工事#1
ヨコハマタイヤマニュファクチャリング(タイランド)の代表取締役社長、水本康博氏は、工場建設の経緯から現在までを次のように語った。
「横浜ゴムは、日本、アメリカ、フィリピン、中国、ベトナムに生産工場を持ち、お客様サービスを第一とし、クオリティの高い製品を製造しています。
世界的なTBS(トラック・バス用タイヤ)の供給体制の強化、販売拡大、低コスト・高品質のTBSの実現を目指し、2003年10月にタイ進出を決定。2004年1月にタイ政府の認可を得て、現地法人を設立しました。
バンコクから南に約120kmの位置にあり、原料の産地や港が近く、インフラが整備された「アマタシティ工業団地」で、2004年5月に着工。2005年4月に生産を開始しました。ここで生産した製品は、北米を中心に欧州、アジア、大洋州、中南米、アフリカなど、世界各国へ輸出しています。
タイ工場の特色は、小規模一環生産方式、画期的な混練工程、徹底した品質保証システムです。特に混練り工程で独自の工法を開発。タイヤの寿命を長くすることで環境への負荷を削減し、環境保護に貢献しています。
高品質で長寿命のタイヤを生産するためには、環境の整備が必要とされるため、工場建物の役割が重要です。工場建設にあたり、当社の購買がインターネット・オークションで入札を実施。建設費が最も低く、建物の品質を確保し、竣工期日を厳守することを条件とし、タイマエダに発注しました。その結果、無駄のない設計で、非常に短い工期をよく守り、強度が高く環境の良い建物を建設し、設備面でも十分な配慮をしてもらい、その技術力に魅了されました。
また、当社はCO2削減対策として『1000年の杜プロジェクト』に取り組んでおり、タイ工場でも2008年に『植樹祭』を行いました。
こうして、当社はタイとともに歩み、タイ人に愛され、タイ人の力で会社を運営し、成功を収めることを目指しています」と語った。
|
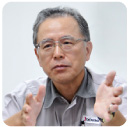 |
ヨコハマタイヤ マニュファクチャリング タイランド 代表取締役社長
水本 康博氏 |
 |
1000年の杜プロジェクト
2008年12月5日(フミポン国王の誕生日)に「植樹祭」を開催。地域の人々とともに7200本を植樹しました。
|
|
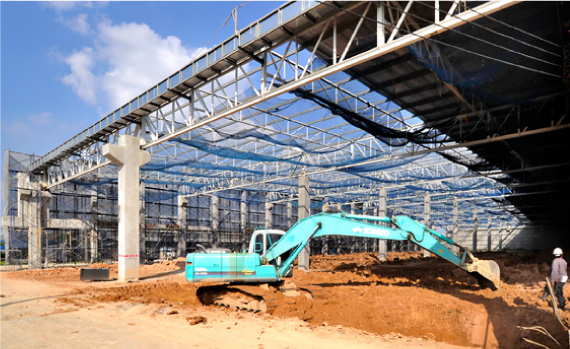
タイマエダは、ヨコハマタイヤマニュファクチャリング(タイ)の工場すべてを受注し、お客様との信頼関係を築いている。タイの多くの物件と同様に、この現場もお客様から直接ご要望をお聞きし、建物がどのように使われるかを把握したうえで、それに基づくプランニングから、見積り、入札、契約、着工、竣工まで、すべてをタイマエダが担当している。
最初に受注したTBS工場第1期工事は、3万m2という大規模な工場だ。2004年4月に設計を詰め、5月に着工。雨季の真っ只中で、地盤改良をしながら基礎を施工するという厳しいものだった。タイは地盤が悪いため、重量のある機械を設置する工場を建設する際は、必ず地盤改良が必要だ。ところが幸運にも、この現場の敷地はアマタシティ工業団地の中でも比較的地盤が良いため、杭打ちなしで施工ができ、工期短縮につながった。屋根、床、壁を急ピッチで施工し、8月中旬の機械搬入に間に合わせた。
タイマエダコーポレーションリミテッドの冨田雄志代表取締役社長は「この工事により、日本人職員だけでなくローカル職員の自信も高めることができ、タイマエダにとって画期的な工事となりました。
このあと引き続き拡張工事を受注し、現在PC・LT工場第1期工事5万m2を順調に建設しています。現在建設中の建物を含めて、建設面積は約14万m2。これほど大規模な工事を手掛けることができたのは、これまでの建設実績をもとにして、短い工期に対応できる施工能力、見積体制、ならびに本店各部署からの支援体制が確立されているからだと思います」と語った。
|
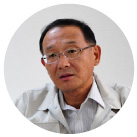 |
タイ マエダ コーポレーション
代表取締役社長
富田 雄志 |
|
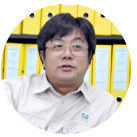 |
タイ マエダ コーポレーション リミテッド
建築部長 戸田 耕資
|
タイに赴任した直後にこの現場のTBS第1期工事の見積担当となり、入札、受注を経て、富田所長(現社長)と2人で現場に乗り込みました。大型工事のため、地元の協力会社を選定し、数社に直接発注して原価改善に取り組みました。この現場は、タイマエ
ダ全体の安全・原価・協力会社・工程の改善や仕事の進め方を大きく変えた「エポックメイキング」だったと思います。今後はさらに品質と安全のレベルを向上させることが目標です。 |
|
|
▼次のページへ